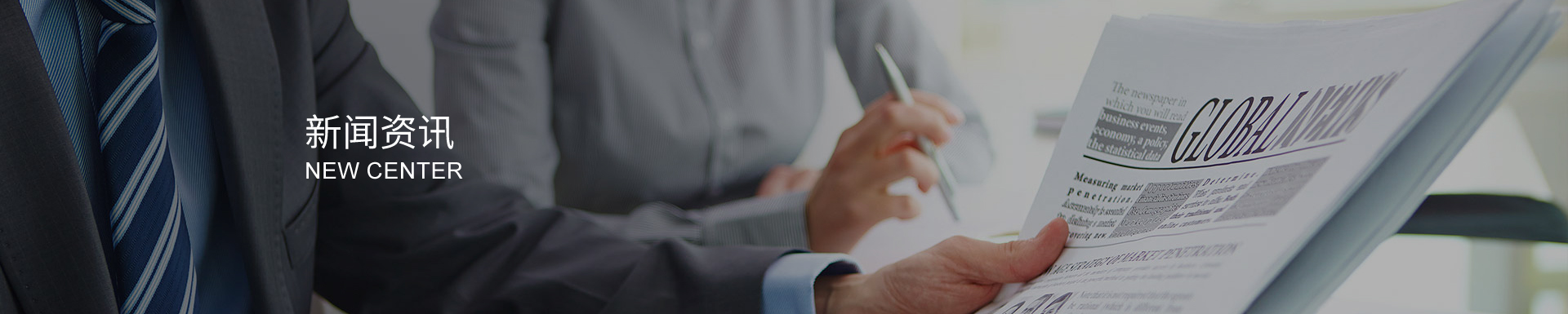
如何進行壓縮機配件的性能測試和驗證?
進行壓縮機配件的性能測試和驗證是一個關(guān)鍵過程,旨在確保這些部件在實際運行中的可靠性和效率。以下是一些基本步驟和方法:
1. 定義測試標(biāo)準(zhǔn)和性能指標(biāo):首先,需要根據(jù)壓縮機的設(shè)計規(guī)范和應(yīng)用需求定義壓縮機配件的性能指標(biāo),如效率、耐用性、容量等。
2. 選擇適當(dāng)?shù)臏y試設(shè)備和環(huán)境:使用專門的測試臺和儀器進行性能測試。確保測試環(huán)境(如溫度、濕度)與壓縮機配件將要操作的實際環(huán)境相匹配。
3. 進行基準(zhǔn)測試:在正式的性能測試之前,進行基準(zhǔn)測試以確定壓縮機配件在標(biāo)準(zhǔn)條件下的行為。這有助于識別出任何設(shè)計或制造上的缺陷。
4. 加載和耐久性測試:對壓縮機配件進行持續(xù)運行測試,以模擬實際工作條件下的負(fù)載。監(jiān)測其在長時間運行后的性能變化,檢查是否有疲勞或損壞跡象。
5. 環(huán)境條件影響測試:考慮到環(huán)境因素對性能的影響,進行溫度循環(huán)測試、濕度測試等,以驗證壓縮機配件在特殊條件下的可靠性。
6. 安全和符合性測試:確保壓縮機配件符合所有相關(guān)的安全和環(huán)境規(guī)定。進行必要的認(rèn)證測試,如CE標(biāo)志或UL認(rèn)證。
7. 效率和能耗測試:測量壓縮機配件在不同操作條件下的能效,評估其整體能耗。
8. 振動和噪音測試:評估壓縮機配件運行時產(chǎn)生的振動和噪音水平,確保它們在可接受的范圍內(nèi),不會影響壓縮機的整體性能。
9. 故障模式和效果分析(FMEA):進行FMEA分析,預(yù)測可能的故障模式及其對系統(tǒng)性能的影響,以便進行必要的改進。
10. 綜合性能評估:將測試結(jié)果與設(shè)計目標(biāo)和用戶需求進行比較,評估壓縮機配件是否滿足預(yù)期的性能標(biāo)準(zhǔn)。
進行這些測試的目的是確保每個壓縮機配件都能在其預(yù)期的工作環(huán)境中表現(xiàn)出較好性能,并且具有足夠的可靠性和安全性。這一過程不僅有助于驗證產(chǎn)品設(shè)計,還可以幫助制造商優(yōu)化生產(chǎn)過程和提高產(chǎn)品質(zhì)量。